In the field of wind turbine blade, carbon fiber is mainly applied to the main beam of wind turbine blade in the form of pulling and squeezing plate.
Compared with glass fiber, the density of carbon fiber is about 30% smaller than that of glass fiber. The V-90 type 3.0MW fan blade produced by wind power giant Vestas has achieved the effect of weight reduction of 32% and 16% lower than that of glass fiber. According to Sandia Laboratory in the United States, after replacing the 100-meter-long wind turbine blade main beam from glass fiber with carbon fiber, carbon fiber accounted for about 12.4% of the blade mass, and the total weight of the blade decreased by 28%, while the material cost only increased by about 9% (the price of carbon fiber for wind power is about $15 / kg). Previously, due to the high cost of carbon fiber, the use of carbon fiber in wind power blades is low. In the future, with the acceleration of the trend of large fan blades and the further reduction of the cost of carbon fiber in the civil field, the permeability of carbon fiber in wind power blades will continue to increase.
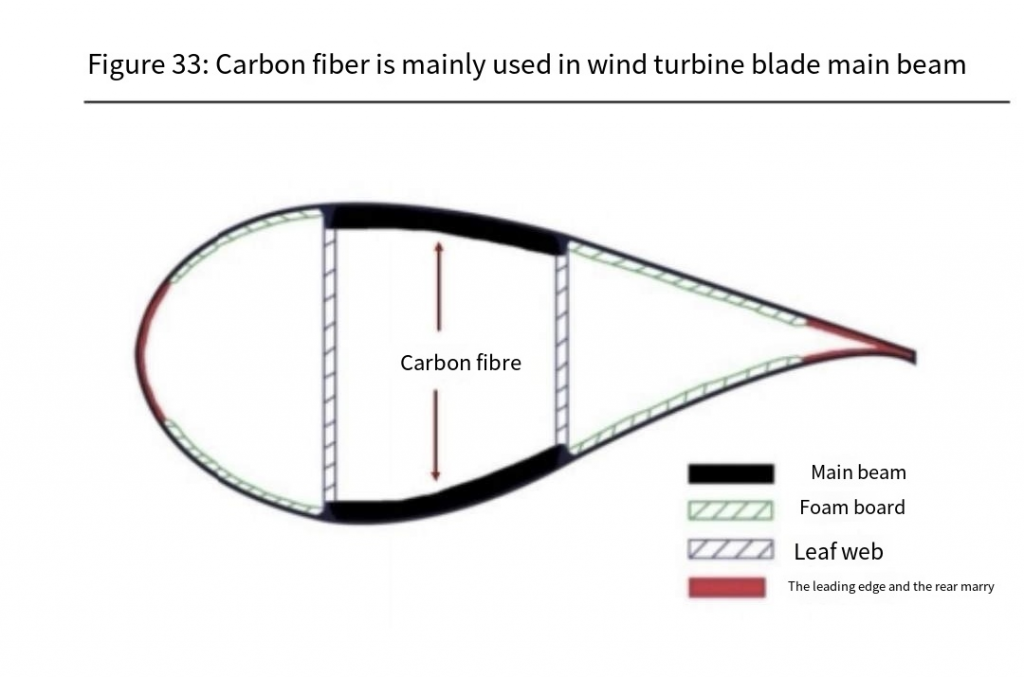
In the aviation field, carbon fiber materials are used in all levels of aircraft structure
Compared with traditional space metal alloy materials, carbon fiber composites have higher specific strength, specific modulus, fatigue resistance and corrosion resistance, and can withstand the pressure and climate conditions of aircraft when flying at high speed. Aviation field of carbon fiber composite materials mainly use hot pressing tank molding process. The good molding ability of carbon fiber composite materials can greatly reduce the structural design cost and manufacturing cost. At present, carbon fiber composites have been successfully used in the aircraft fuselage, wings, engine fan blades and shell, engine cabin, engine cabin materials and other levels.
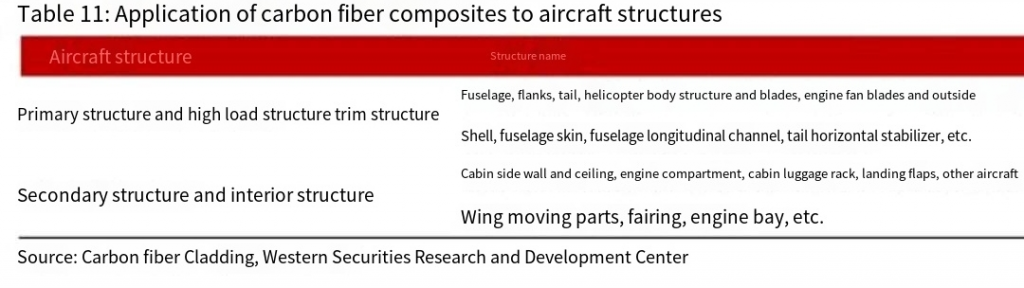
In large civil aircraft, the amount of carbon fiber composite material has exceeded 50%. In the aerospace carbon fiber demand, the need for commercial aircraft
The proportion has exceeded 50%. With the upgrading of civil aircraft, the application of carbon fiber composites in aircraft has gradually increased
In addition, the amount of carbon fiber composite materials used on Boeing B787 and Airbus A350 has reached or even more than 50%, replacing them
Aluminum alloy becomes the most used material. China's independent research and development of the C919 large passenger aircraft, the realization of advanced materials in the domestic people
For the first large-scale application of the machine, the amount of carbon fiber composite materials of the whole machine exceeded 12%, and is expected to further increase to 25% in the later stage.
In the future, the amount of CR929 carbon fiber composites jointly developed with Russia will reach more than 50%.
In the post-epidemic era, the civil aviation industry is expected to reach an inflection point of recovery. Since the outbreak, the global civil aviation travel demand has suffered
Boeing and Airbus as global air traffic fell about 63% in 2020 from 2019, according to Thiel Group
The capacity of related composite aircraft has been reduced to cope with declining demand. With the normal trend of the epidemic and the global epidemic
With the increase of seedling vaccination rate, the demand for civil aviation travel is expected to gradually recover, based on the epidemic and the complex and lagging aviation field
Civil aviation is expected to recover to 2019 demand levels around 2024. According to the Mayo carbon fiber forecast,
In 2025, the global aerospace industry carbon fiber demand will reach 26,000 tons, with a five-year CAGR of 10%.
According to Boeing's Civil Aviation Market Outlook for China, 25 percent of the global aviation growth in the past decade came from China
In China, this trend will continue over the next 20 years, with more than 8,000 new aircraft delivered by 2040.discuss
Fly is more optimistic, with more than 9,000 aircraft by 2040, when China will become the world's largest aviation market. In the fly
In the development trend of lightweight aircraft, it will certainly drive the strong demand of carbon fiber in the civil aviation industry.
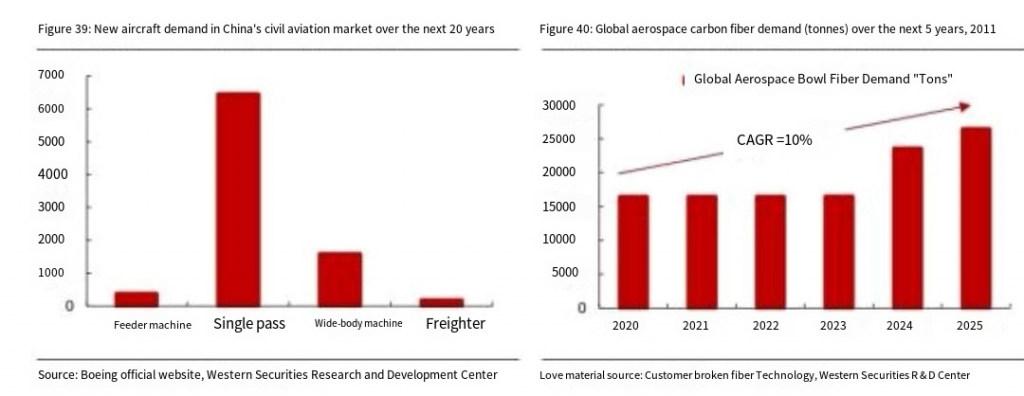
The release of domestic large aircraft orders, drive carbon fiber composite demand continued to increase. At present, China's six C919 test aircraft all first
As the first order is expected to be delivered in early 2022, the current total number of orders has exceeded 1,000 (including intended orders).
Construction of the CR929 jet began in September 2021 and could make its first flight in 2025. At the annual capacity of 100 units per year
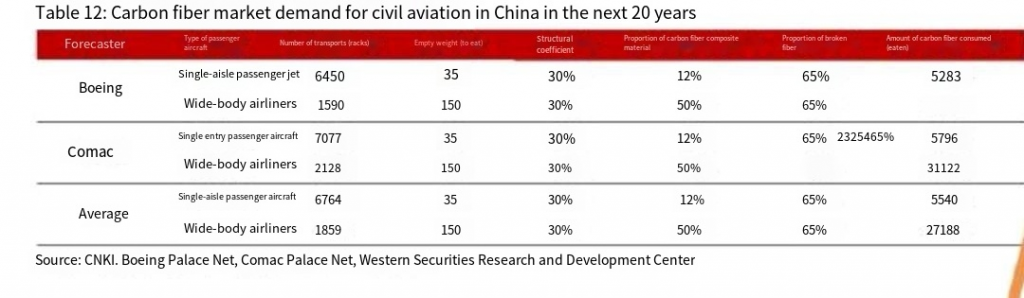
It is estimated that in the next 20 years, China's C919 and CR929 large aircraft will add 2,000 and 500, respectively
Rack, the corresponding carbon fiber demand will reach 9500 tons, an annual demand of 473 tons. With the commercialization of domestic passenger aircraft
Entering, domestic aircraft will gradually realize import substitution, and increase the demand space for domestic carbon fiber and its composite materials.
In the field of automobile, carbon fiber composite material has a significant effect on energy saving, emission reduction and endurance improvement of automobile.
Similar to the aviation industry, the lightweight of the automotive industry can bring great economic benefits and performance improvements. According to the European Aluminum Association, when the quality of cars is reduced by 10%, the efficiency of energy use can be increased by 6-8%, reduce emissions per 100 kilometers by 10%, and increase tire life by 7%. For fuel vehicles, when the vehicle quality is reduced by 100 KG, it can save the fuel consumption of 0.3-0.6L/ 100 km, and then reduce the carbon dioxide emission of 10g / km; for new energy vehicles, the weight reduction of 100 KG can increase its endurance by about 6% -11%.besides,
For hydrogen cars, some models of hydrogen storage bottles have begun to use carbon fiber materials, compared with traditional type I bottles and bottles,
The bottles and bottle greatly increase the pressure and hydrogen storage density that the hydrogen storage bottle can withstand, which means the energy under the same volume
Enough to store more hydrogen to improve the car's range.
Carbon fiber composite material improves the mechanical properties of the structure, and makes the overall quality of the body greatly reduced. With ordinary steel
In contrast, carbon fiber composites can reduce weight by about 60%, compared with the lightweight magnesium aluminum alloy with relatively poor mechanical properties
10% to 20%. At the same time, the excellent corrosion resistance and flame retardant properties of the carbon fiber composite material make it into one
Step to become the ideal alternative material for light power battery box for new energy vehicles. In 2020, Germany and BMW Group respectively
Nio and other companies cooperate with us to mass manufacture electric car battery cases. In the global new energy vehicle penetration rate is rapidly increasing when
Next, the carbon fiber demand will be gradually released.
With the increasing number of application models, the body structure may become the largest application part in the future. The F1 racing car of the 19 50s was
The automotive sector was the first vehicle to use carbon fiber composites. With the improvement and perfection of the related manufacturing process, the carbon fiber composite
The material has gradually realized the penetration from professional racing cars to high-performance luxury cars and then to popular cars, among which the earliest application of carbon fiber
The composite and mass-produced mass model is the BMW i3, and the life module of the main body uses carbon fiber composite material
Material, achieved 250-350 kg of weight loss. At present, carbon fiber composite materials are mainly used in sound insulation board, front-end bracket and car
Body chassis and seat structure, with the further reduction of future application costs, carbon fiber composite materials may be in the body structure,
Chassis components, steering and suspension system and other components to achieve large-scale application, in which the proportion of body chassis structure is expected to use from
The current 13% is up to 55%.
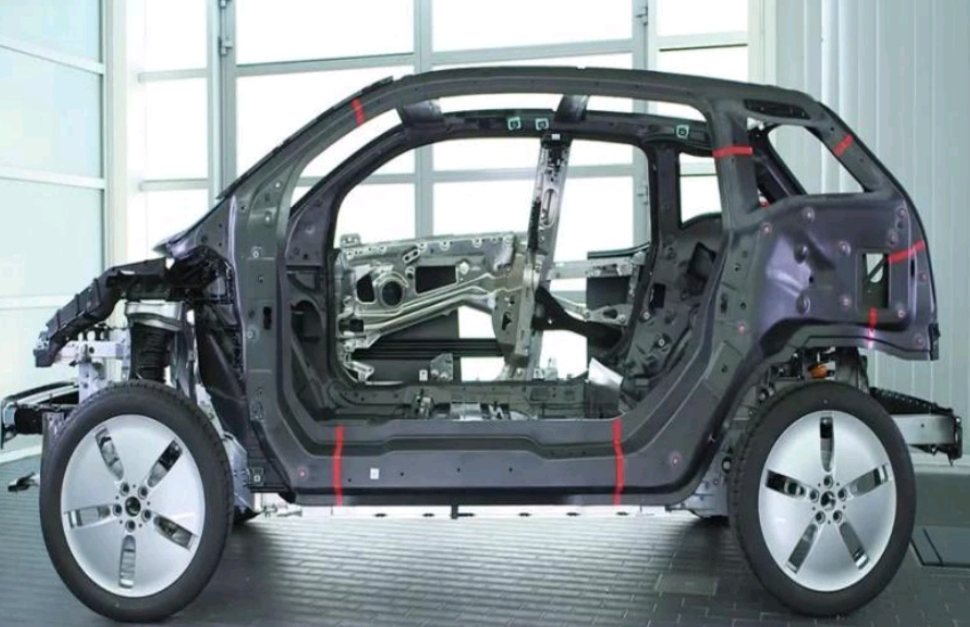
BMW i3 carbon fiber body
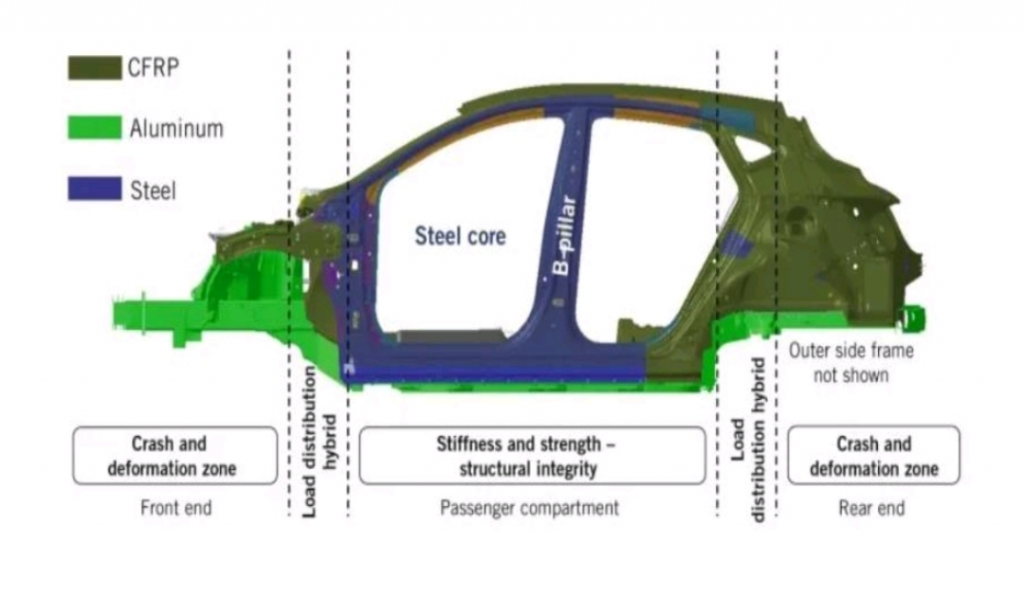
Changan's first carbon fiber-aluminum alloy hybrid body has been successfully trial-produced
The permeability of carbon fiber composites is expected to further increase along with the reduction of manufacturing and processing costs. Although the carbon fiber composites in the No
Body weight reduction, mechanical properties and many other aspects have significant advantages, but currently restricts its large-scale application in automotive materials
The factor still lies in its high cost and processing difficulty. Its price is ten times higher than glass fiber composite materials, compared to high strength steel
There is also an obvious gap with magnesium aluminum titanium alloy, and the high process difficulty also limits its rapid and continuous production process, so
Current models using carbon fiber composites are still high-end.
At present, the new industrialization alliance mode of "automobile manufacturer + CFRP parts supplier" has begun to rise. As in the Prodrive
The company and BMW actively cooperated with CFRP manufacturing enterprises in the production of i3
Parts manufacturing and processing cost. Under this cooperation mode, RTM process is widely used, and the vehicle production gradually realizes modularization,
The number of parts is 2 / 3 less than that of traditional metal parts, the assembly rhythm becomes very fast, and the length of the assembly line is correspondingly large
Reduce, and make the input cost of the final assembly line significantly reduced. In recent years, new forming processes such as HP-RTM,
T-RTM and other original molding process are constantly upgraded and optimized. In the production and assembly of automotive carbon fiber composite materials, the materials are made of
This accounts for about 30%, and with the rise of the alliance model, we expect the production of carbon fiber composite components in the future
It is expected to gradually decrease, and its penetration rate in vehicle materials is expected to continue to increase.
Demand for automotive carbon fiber is growing rapidly and is expected to exceed 20,000 tons by 2024. According to the forecast of the China Association of Automobile Manufacturers, the production of new energy vehicles will still maintain a high growth rate in the next five years, and the global and Chinese production of new energy vehicles will reach respectively in 2025
18 million and 8 million vehicles. According to the plan of the Energy Saving and New Energy Vehicle Technology Roadmap (version 2.0), 2035
It is expected that the lightweight factor of fuel passenger vehicles will be reduced by 25%, and the lightweight factor of pure electric passenger vehicles will be reduced by 35%.
Considering the continuous increase in weight reduction demand for new energy vehicles and the continuous decline in the processing and manufacturing cost of automotive carbon fiber composites,
In the future, the demand for automotive carbon fiber will maintain rapid growth. According to the Mayo carbon fiber forecast, according to the 10% CAGR, it is expected to be 2025
The annual global demand for automotive carbon fiber will reach 20,226 tons.
In the field of sports, China's sports and leisure industry has a large demand for carbon fiber, and golf clubs, bicycles and fishing rods are the main application directions.
The field of sports and leisure is one of the earliest application fields of carbon fiber. Nearly 90% of the world's carbon fiber sports equipment is processed in mainland China
With Taiwan, China completed, sports and leisure in the global carbon fiber application demand accounted for 14% in 2020, while in China
Demand accounted for nearly 30%. The product category is wide, mainly 3K, 12K and other small silk bundles, the unit price is stable.
The excellent characteristics of carbon fiber perfectly fit the special requirements of sports equipment in the process of sports. First, the carbon fiber composite is light
The characteristics of high quality make it suitable for the training of high strength but light quality requirements of sports equipment, such as hockey clubs;
Secondly, its special microscopic crack structure makes it have very good shock absorption properties; finally, carbon fiber composite has very high
Safety, when the load beyond the tolerance range does not occur direct fracture, even if part of the structure fracture will not make it
His carbon fiber doesn't work well. Therefore, carbon fiber composites have been widely used in the sports industry, which is high
Rove club, bicycle and fishing rod are the most important application directions, which together account for 75%.
The increase in the number of athletes and the increased demand for equipment has driven a steady increase in the demand for carbon fiber. In the "healthy China" strategy
Under the background of continuous promotion and continuous improvement of people's health awareness, the era of national movement is coming, which is a frequent country in recent years
The number of people participating in sports has increased year by year, reaching 435 million in 2020, and the growth rate is increasing continuously. Use of a superior performance of the one
Sports equipment can get a better sports experience, and the increase in the number of athletes will increase the demand for carbon fiber composites for sports.
According to the forecast of the Mayo carbon fiber, the demand for carbon fiber in the sports and leisure sector will grow steadily to 19,655 tons for five years in 2025
The CAGR was 5%.
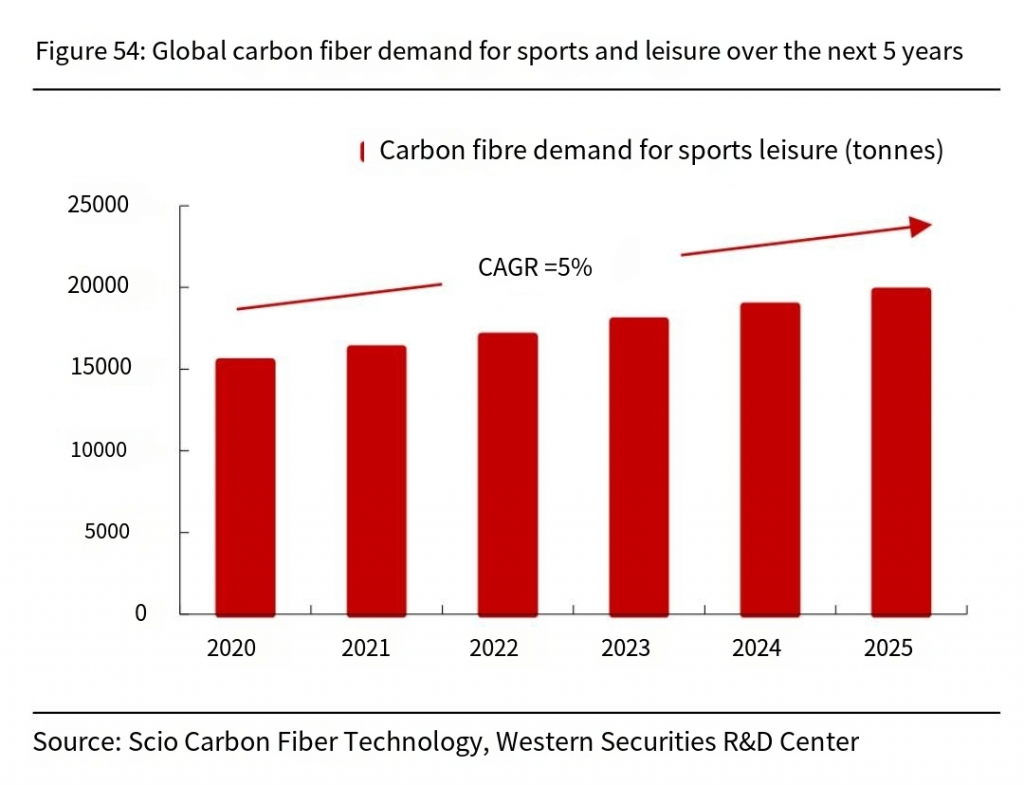